Microesferas de vidrio huecas
Polypedia > ► Cargas minerales y Fibras > ► Cargas minerales > ► Microesferas
Microesferas de vidrio huecas
¿Qué son las burbujas de vidrio?
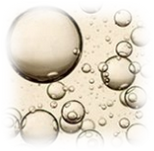
Composición de las microesferas de vidrio huecas
Las microesferas de vidrio huecas forman un polvo de color blanco que consta de pequeñas burbujas con diámetros que oscilan entre 21-151 μm con espesores de pared de menos de 1 μm. La composición del vidrio y la forma esférica casi perfecta de las microesferas proporcionan una alta resistencia a la compresión. Se pueden distinguir dos principales niveles de HGM : de alto y bajo grado en su forma y estructura. Los HGM de bajo grado osea de menor calidad fallan con menos carga, de manera menos predecible, en comparación con los HGM de alto grado osea de alta calidad. La densidad de las burbujas de vidrio varía de 0,15 g/cc a 0,60 g/cc. A diferencia de otras cargas minerales como la fibra de vidrio picada, el carbonato cálcico y el talco, el volumen por unidad de peso es por tanto mucho mayor. Reemplazar los rellenos inorgánicos por Glass Bubbles da como resultado piezas compuestas con densidad reducida. Por ejemplo, 1 kg de material de burbuja de vidrio típico tiene un volumen de 5000 cm3 , mientras que el peso equivalente de CaCO3 desplaza solo 370,4 cm3. Debido a las densidades extremadamente bajas de las burbujas de vidrio, la formulación, por lo tanto, debe basarse en volumen en lugar de peso. Si simplemente se sustituyera un peso igual de burbujas de vidrio por el carbonato de calcio en una formulación, la proporción de volumen de todos los demás ingredientes se reduciría sustancialmente. La formulación por volumen en lugar de peso permite el equilibrio adecuado de resina, relleno y refuerzo, por lo que los componentes se pueden hacer más livianos mientras se mantiene un buen equilibrio de propiedades físicas. Las burbujas de vidrio ocupan hasta 20 veces más volumen por unidad de peso en comparación con los rellenos minerales como el talco y el carbonato de calcio. Un ejemplo más antiguo pero útil del uso de Glass Bubbles para controlar con precisión el peso de la pieza final se puede encontrar en la fabricación de bolas de boliche. Aquí, los núcleos internos de las bolas de boliche se preparan con una resina de poliéster fundida. Cuantas más burbujas de vidrio se utilicen en la resina, menor será la densidad de la bola de boliche. Por lo tanto, el peso final de la bola de boliche se puede ajustar con precisión y facilidad ajustando la concentración de volumen de las burbujas de vidrio en la resina. Es importante destacar que la adición de Glass Bubbles no afecta la estabilidad de la resina y la mezcla de resina sigue fluyendo libremente. Como destaca este simple ejemplo, Glass Bubbles tiene más que ofrecer materiales compuestos avanzados además de la obvia reducción de densidad.
Las burbujas de vidrio son huecas
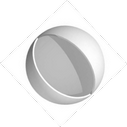
Las burbujas de vidrio son esféricas

Partículas esféricas
Las microesferas son partículas esféricas que se pueden distinguir en dos categorías; sólido o hueco. Las microesferas típicas varían de 1 a 200 μm de diámetro. Las microesferas están hechas de vidrio, cerámica, carbono o plástico, según las aplicaciones. Las cargas sólidas en partículas generalmente aumentan tanto el módulo de Young como la densidad de los polímeros. La incorporación de microesferas huecas en los polímeros no necesariamente reduce la densidad, eso depende del material del que están hechas las microesferas y del grosor y volumen de su pared, pero puede permitir un mejor equilibrio entre las propiedades mecánicas y la densidad. También puede haber algunos beneficios incidentales en términos de procesamiento y calidad de la superficie. Las microesferas están hechas comúnmente de vidrio, pero también se han utilizado diversos termoplásticos, resina fenólica, carbono y cerámica. Son capaces de mejorar las características de flujo de un polímero en el molde, y la viscosidad de la resina aumenta solo ligeramente al aumentar el contenido de relleno. También reducen la contracción del moho. Las calidades de vidrio ahora disponibles comercialmente varían mucho en cuanto al grosor de la pared, el tamaño medio y la distribución del tamaño. Como resultado, se puede lograr una amplia gama de propiedades y características de procesamiento con una fracción de volumen de relleno dada. Recientemente, se han producido microesferas hechas de polímero resistente a los gases y que contienen hidrocarburos líquidos. Cuando las microesferas se agregan a una resina y se calientan, las microesferas se expanden, dando una densidad muy baja. Existen dificultades en el uso de partículas de relleno huecas. Las calidades de paredes muy delgadas que afectarían la densidad más baja y el peso del producto se trituran fácilmente durante el moldeo por inyección. Cuando se rompen, los fragmentos no solo aumentan la densidad, sino que también desgastan el equipo y actúan como concentraciones de tensión, con efectos adversos en el inicio de la grieta en los plásticos llenos. Los espesores de pared de las microesferas huecas están típicamente en el rango de 0.4 a 1.51 micron. Cuando se incorporan burbujas de vidrio en resinas líquidas de baja viscosidad, tienden a migrar hacia la superficie, ya que son menos densas que la resina, dejando un contenido de relleno inadecuado en el resto del material.
Propiedades de las microesferas de vidrio huecas
Propiedades clave de la microesferas de vidrio huecas , son baja absorción de agua, baja conductividad térmica, alta resistencia química y transparencia de radio. La buena adhesión de los HGM a los aglutinantes poliméricos los hace ideales para composites que brindan una combinación única de propiedades. Todos los factores mencionados anteriormente definen una amplia variedad de aplicaciones para las HGM. Las burbujas de vidrio son huecas y, por lo tanto, reducen la capacidad calorífica de la resina y, a su vez, el coeficiente de expansión térmica lineal (CLTE). También tienen conductividades térmicas bajas, tan bajas como 0.05 W • m -1 • K -1 a 20°C. Por ejemplo, la reducción de masa a su vez reduce la capacidad calorífica de la resina , lo que a su vez da como resultado tiempos de enfriamiento más cortos permitiendo que las piezas se produzcan más rápidamente. Además, el coeficiente de expansión térmica lineal (CLTE) del material compuesto disminuye. El bajo CLTE significa que se pueden fabricar piezas compuestas más grandes, y estas son menos propensas a deformarse durante el enfriamiento, también conocido como alabeo. El bajo CLTE también puede aportar beneficios en las piezas acabadas. Por ejemplo, las piezas sólidas diseñadas con burbujas de vidrio (por ejemplo, molduras de techo) serán menos propensas a agrietarse cuando se exponen a ciclos de frío/calor. La naturaleza hueca de Glass Bubbles impacta aún más la interacción del compuesto con las ondas de luz y sonido. Esta propiedad encuentra su uso en aplicaciones especializadas como la amortiguación acústica . Las burbujas de vidrio pueden soportar altas presiones externas debido a su forma esférica y composición química. La resistencia de las burbujas de vidrio cuantificada como la resistencia al aplastamiento isostático, que depende del grado y varía entre 100 y 30000 PSI. Dado que la resistencia al aplastamiento de un grado específico depende en gran medida del grosor de la pared, la resistencia al aplastamiento y la densidad del grado están inversamente relacionadas. Como resultado, la selección de un grado de burbuja de vidrio para una aplicación específica generalmente está determinada por la resistencia al aplastamiento requerida para sobrevivir al procesamiento durante la fabricación de la pieza.
Tecnología de fabricación para microesferas de vidrio huecas
La tecnología para la fabricación de HGM es una combinación de complejos procesos hidrodinámicos y químicos que tienen lugar en el curso de la formación de burbujas huecas sopladas a partir de micropartículas de vidrio fundido. Una dosis exacta de gas en el polvo fundido sopla microesferas con el diámetro y el espesor de pared requeridos. Con un proceso tecnológico tan complejo, es imposible hacer microesferas con un diámetro predeterminado estrictamente idéntico. Por tanto, la calibración de las microesferas se realiza de acuerdo con sus dimensiones. La resistencia de las microesferas se establece probando la presión hidrostática a la que no falla más del 10% de los HGM. Es natural que las microesferas con mayor densidad, y por lo tanto con paredes más gruesas, sean más fuertes.
Aplicaciones para microesferas de vidrio huecas
Las aplicaciones para microesferas de vidrio huecas se desarrollan constantemente. Por ejemplo:
- Los HGM aumentan considerablemente el rendimiento de los explosivos, mientras que la incorporación de HGM en el blindaje proporciona una capa de atenuación de explosiones muy eficaz;
- en lodos de perforación, los HGM intensifican el proceso de perforación al tiempo que aumentan considerablemente el ciclo de vida del equipo de perforación;
- la incorporación de HGM en el mortero de cemento permite producir materiales aislantes térmicos sin contracción y de endurecimiento rápido;
- Los HGM permiten reducir considerablemente la densidad de los materiales del compuesto de moldeo en láminas (SMC) y del compuesto de moldeo a granel (BMC), por ejemplo de 1,8 g/cm3 a 1,3 g/cm3 , sin una reducción detectable de la elasticidad o resistencia de los compuestos.
Hoy en día, los HGM se utilizan ampliamente para fabricar masillas y compuestos especiales. Pero el campo de aplicación más interesante para ellos es la creación de compuestos sándwich súper fuertes.
Nuevas posibilidades
Las superficies exteriores de los materiales compuestos son las áreas bajo carga máxima; más lejos de la superficie de un compuesto multicapa, donde las tensiones son menores, se pueden utilizar materiales de menor resistencia y menor densidad. Los compuestos multicapa (sándwich) proporcionan un aumento apreciable en el espesor de la estructura y, como resultado, aumentan drásticamente su resistencia y especialmente su rigidez sin un gran aumento de peso.
Las estructuras sándwich multicapa tradicionales se pueden clasificar en dos categorías principales: las que utilizan materiales de núcleo de panal; y los que utilizan núcleos de espuma ligera. Cada uno tiene sus ventajas y desventajas y debemos elegir el campo de aplicación más eficiente para ellos. Los núcleos de espuma y nido de abeja nos permiten hacer composites sándwich con características específicas de rigidez muy altas, pero la baja resistencia al cizallamiento y la rigidez de estos núcleos tradicionales no nos permiten utilizar la fuerza de las caras al máximo efecto, y como resultado el total El potencial de los compuestos sándwich de hoy en día no se realiza. Este inconveniente se ve claramente y es más pronunciado cuando se hacen estructuras finas en sándwich. En este caso, para obtener una alta resistencia y rigidez de los bocadillos delgados, se deben utilizar caras hechas de materiales con altas características de elasticidad y resistencia. Al hacerlo, el espesor del núcleo es comparable al espesor de la cara, lo que exige mayores propiedades de cizallamiento del material del núcleo. Ésta es la razón por la que, hasta ahora, los bocadillos a base de panal y espuma no se utilizan mucho a la hora de hacer estructuras relativamente delgadas y a la vez resistentes. Ilustraremos esto tomando como ejemplo una tabla ordinaria. Si una tabla no asegura la resistencia y rigidez necesarias, la forma más sencilla de asegurar esto es colocar una tabla encima de otra. Como resultado, creamos una estructura sándwich de dos capas (Figura 6a), y cuando las capas (tablas) no están unidas entre sí y la estructura está doblada, las tablas simplemente se desplazan una referencia a otra. En este caso cada tablero trabaja de forma independiente y tenemos ordinaria doble resistencia y rigidez de la estructura. Después de unir las tablas con pegamento, o simplemente con clavos, para evitar el cizallamiento, es posible que trabajen juntas y formen una estructura considerablemente más fuerte (dos veces) y más rígida (cuatro veces) (Figura 6b). Es esencial que la fuerza de la conexión entre las capas sea lo suficientemente alta para que las tablas funcionen juntas. Cuanto más fuerte y rígido sea el material del que están hechas las tablas, mayor será la tensión de corte que se produce en la capa de conexión. Este ejemplo puede servir para ilustrar un sándwich de tres capas en el que las funciones de los tableros se cumplen por las caras y el pegamento por el núcleo ligero. La diferencia es que en este caso las tablas (caras) son relativamente delgadas y la capa de pegamento (el núcleo) en un compuesto de espuma o sándwich de panal es más gruesa. Por lo tanto, queda claro que para que todas las capas de la estructura en sándwich trabajen juntas, es necesario tener una cierta resistencia mínima al corte en el núcleo.
El hecho de que el compuesto sándwich no se doble puede deberse a dos razones básicas. En primer lugar, la falla de las caras cuando la carga excede la resistencia última del material y, en segundo lugar, la falla del núcleo cuando se somete a la resistencia máxima al corte. Idealmente, en una estructura mixta sándwich óptima, la falla de las caras y el núcleo debe ser simultánea, pero generalmente no funciona así. Comúnmente, la falla de la estructura de múltiples capas ocurre cuando una o más de las capas no ha agotado su potencial de resistencia, o una capa falla antes que las otras.
La mayoría de los compuestos actuales se fabrican con caras relativamente delgadas hechas de materiales con características de elasticidad y resistencia relativamente bajas porque, como se mencionó anteriormente, las propiedades de bajo cizallamiento de los núcleos tradicionales (plásticos de panal y espuma) no permiten todo el potencial de la alta resistencia. caras que se utilizarán. En otras palabras, cuando se logran esfuerzos cortantes limitados para un material dado en el núcleo, el aumento de la resistencia y la rigidez de las caras no da como resultado un aumento de la resistencia de toda la estructura en sándwich.
Para que funcionen todas las capas sandwich, es necesario tener una cierta resistencia mínima al corte en el núcleo. También es cierto que cuanto mayor sea la resistencia y rigidez de las caras, más importante es tener características de alto cizallamiento en el núcleo. En la actualidad, se han desarrollado modelos matemáticos que describen el comportamiento de compuestos cargados de múltiples capas. Estos nos permiten formular requisitos en cuanto a las características de elasticidad y resistencia de las capas en una estructura compuesta multicapa dependiendo de su geometría y condiciones de carga.
Ventajas
La mayor ventaja de las microesferas de vidrio huecas sobre otras cargas es su muy baja densidad, que es típicamente 0.1 ± 0.7 g cm73. En comparación, la densidad de las microesferas de vidrio sólido es de 2.54 g cm73. El diámetro exterior de las microesferas de vidrio huecas está en el rango de 40 ± 125 mm y el grosor de la pared es de solo 1 ± 2 mm. Bajo altas presiones de moldeo en moldeo por inyección u otras operaciones de moldeo, las microesferas de vidrio huecas tienden a romperse. Esto limita su uso a procesos de moldeo a baja presión que generalmente se usan para polímeros termoestables. La resistencia al aplastamiento de las microesferas de cerámica huecas es mejor ya veces se usan en lugar de las microesferas de vidrio huecas. Las microesferas de vidrio o cerámica huecas se utilizan para producir espumas sintácticas en polímeros termoestables como los epóxicos. En las espumas convencionales, los agentes de expansión químicos crean la estructura celular. En las espumas sintácticas, la estructura celular se debe a la presencia de microesferas huecas. Las espumas sintácticas son mucho más rígidas y resistentes que las espumas convencionales y a menudo se usan como material central para estructuras sandwich de alto rendimiento que contienen laminados de fibra de carbono / epoxi en las pieles.
Producción
Las microesferas generalmente aparecen como un polvo blanco que fluye muy fino. Los vidrios generalmente están hechos de vidrio de vidrio de borosilicato de cal sodada, o vidrio con alto contenido de sílice, que en un proceso se calienta pasando a través de una llama, junto con un agente de soplado químico para generar gas, y las esferas resultantes tienen diámetros medios en el rango 5 a 90 micron. Otro método de producción consiste en soluciones de secado por atomización de silicato de sodio. Las microesferas cerámicas pueden fabricarse como un subproducto de la combustión del carbón. Las microesferas de carbono se preparan calentando materiales orgánicos adecuados con un agente de expansión. Las burbujas de vidrio son vulnerables a ácidos y álcalis fuertes, pero por lo demás su resistencia química es buena. Se puede aplicar un tratamiento de superficie de silano o titanato para mejorar la adhesión a un polímero.
Las microesferas huecas de polímeros se preparan principalmente mediante tres enfoques: autoensamblaje, síntesis asistida por plantilla y polimerización en emulsión. El autoensamblaje y la síntesis asistida por plantillas exigen un sistema de reacción y procedimientos de procesamiento, mientras que la polimerización en emulsión es más amigable y escalable en la industria. Además, este método de polimerización en emulsión puede controlar eficazmente el tamaño, la estructura y la composición de la esfera. Por lo tanto, la polimerización en emulsión es un método ideal para preparar microesferas huecas de polímeros, especialmente a gran escala. En los últimos años, la preparación de microesferas poliméricas mediante secado por pulverización ha llamado la atención, en la cual se emplea un atomizador para hacer pequeñas gotas con la evaporación instantánea posterior por aire caliente para obtener microesferas. En comparación con otros métodos, el secado por pulverización tiene las ventajas de un proceso fácil, alta capacidad de control y facilidad de comercialización. Sin embargo, preparar microesferas huecas con un tamaño y una morfología controlables mediante secado por pulverización sigue siendo un desafío.
Compound
Las microesferas de vidrio huecas se pueden agregar a las poliolefinas como una forma de endurecer el sistema de resina y al mismo tiempo reducir sustancialmente su densidad. Las microesferas que se usan como rellenos de plástico tienen típicamente una densidad de solo 0.6 g / cm3, mucho más baja que los rellenos estándar (con densidades de 2.7 2.9). La baja densidad ayuda a que las esferas sean rentables en volumen, y se traduce en densidades de PP lleno tan bajas como 0.8 g / cm3 cuando se carga con 30% de esferas (por volumen). Usado típicamente en plásticos con un tamaño de partícula de alrededor de 16 30 micras de diámetro, se dice que el efecto de "rodamiento de bolas" de las esferas de vidrio facilita el flujo de fusión y el enfriamiento del compuesto, a diferencia de otros rellenos que aumentan la viscosidad. Según los informes, las esferas también reducen los tiempos de ciclo (en comparación con los compuestos llenos de talco), la contracción de moldeo y la expansión térmica lineal (CLTE), al tiempo que aumentan el módulo y la resistencia a la flexión. En un estudio de moldeo por inyección que compara un 20% (en peso) de una pieza de PP con microesferas de 16 micras con un 20% de PP con talco, la densidad del PP con relleno de esfera fue casi un 19% menor, lo que se tradujo en un 17% reducido peso parcial Además, la contracción de la parte llena de microesferas se redujo en todas las direcciones en comparación con la parte llena de talco. Y dado que las microesferas permiten que la pieza se enfriara más rápido, el tiempo de ciclo se reduje de 3 segundos.
Procesameinto
Un problema que ha retrasado el uso de microesferas en plásticos ha sido su rotura bajo condiciones de procesamiento estándar. Sin embargo, en los últimos años, las mejoras en el proceso de fabricación han creado microesferas más pequeñas de 16 micras que son lo suficientemente fuertes como para resistir las mayores presiones y fuerzas de los compuestos de plástico o el moldeo por inyección. Aún así, se deben tomar algunas precauciones en el procesamiento, como la alimentación lateral de las esferas más abajo en el tornillo en lugar de con la resina en la tolva y presiones de empaquetamiento más bajas durante el moldeo. El tamaño de las microesferas también afecta las propiedades mecánicas; Las esferas de 16 micrones proporcionan un mayor impacto Izod con muescas y mayor resistencia a la tracción que las esferas. Y, al igual que otros rellenos inorgánicos, los agentes de acoplamiento de silano mejoran la unión del relleno de vidrio hidrofílico al polímero, mejorando el impacto y la resistencia a la tracción en aproximadamente un 40% sobre los compuestos de microesferas no tratadas. Según los informes, los agentes de acoplamiento también aumentan el alargamiento dramáticamente y reducen la rotura de la esfera durante el procesamiento.
Aplicaciones
La industria automotriz, en particular, adoptó la tecnología Glass Bubble, ya que las piezas más ligeras se traducen en una mejor economía de combustible. En automóviles y camiones, las burbujas de vidrio se pueden encontrar en partes compuestas como paneles exteriores de la carrocería, techos, reflectores de faros, deflectores de viento, guardabarros, tablas del piso, puertas de acceso y paneles internos como carcasas de motores y pozos de llantas de repuesto. Si bien las burbujas de vidrio son más conocidas por su capacidad para reducir el peso de las piezas, esto está lejos de ser su única característica. Las aplicaciones modernas en materiales compuestos se basan en la capacidad de Glass Bubbles para mejorar el procesamiento y mejorar las propiedades de las piezas finales del material compuesto. Las mejoras de procesamiento generalmente se refieren a la capacidad de producir piezas a mayor velocidad de producción y con mayor facilidad. Las mejoras en las propiedades se refieren a funcionalidades complementarias aportadas por Glass Bubbles. Estos pueden ser extremadamente diversos, que van desde propiedades mecánicas (rigidez) hasta propiedades retardantes del fuego, acústicas y amortiguadoras y propiedades de aislamiento térmico.